Backflow Prevention Devices Explained
Understanding Backflow Prevention
To protect your water supply from contamination, it’s crucial to understand the concept of backflow and the importance of implementing backflow prevention measures.
What is Backflow?
Backflow occurs when the flow of water in a plumbing system is reversed, causing non-potable water (contaminated or polluted water) to flow back into the clean water supply. This reversal can happen due to a drop in water pressure or a change in the water supply system.
Backflow can lead to the contamination of drinking water with substances such as chemicals, fertilizers, bacteria, or other pollutants. This poses a serious health risk to consumers and can result in waterborne illnesses or other harmful effects.
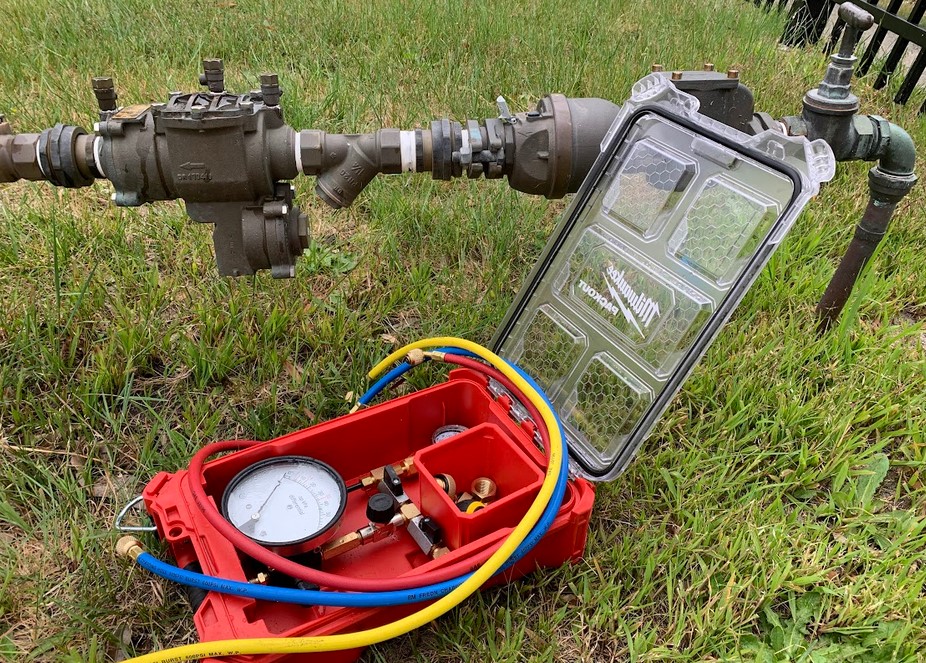
The Importance of Backflow Prevention
Backflow prevention is essential to safeguard the integrity and safety of our water supply. By installing backflow prevention devices in the plumbing system, the risk of backflow and subsequent contamination can be significantly reduced.
Backflow prevention devices are designed to prevent the reversal of water flow and ensure that only clean, potable water enters the water supply system. These devices work by creating a physical barrier or employing a one-way valve mechanism to prevent backflow from occurring.
By implementing backflow prevention measures, we can protect the health and well-being of individuals and communities. It is important to note that backflow prevention devices should be installed and maintained by qualified professionals who are knowledgeable about local regulations and the specific requirements of your plumbing system. Regular testing and maintenance of backflow prevention devices are also crucial to ensure their proper functioning and effectiveness.
Common Backflow Prevention Devices
When it comes to backflow prevention, various devices are available to safeguard the quality and purity of your water supply. These devices work by preventing the reverse flow of water, which can contaminate the potable water system. In this section, we will explore four common backflow prevention devices: Atmospheric Vacuum Breaker (AVB), Pressure Vacuum Breaker (PVB), Double Check Valve Assembly (DCVA), and Reduced Pressure Zone Device (RPZD).
Atmospheric Vacuum Breaker (AVB)
An Atmospheric Vacuum Breaker (AVB) is a simple and cost-effective backflow prevention device. It consists of a one-way valve that allows air to enter the system when there is a drop in pressure, preventing backflow. The AVB is typically installed on individual water outlets, such as hose bibs and irrigation systems. It is suitable for low-hazard applications and must be installed at least six inches above the highest point of water usage. Regular inspection and testing are necessary to ensure proper functioning.
Pressure Vacuum Breaker (PVB)
A Pressure Vacuum Breaker (PVB) is another commonly used backflow prevention device. It consists of two one-way valves separated by an air gap. The PVB is installed at the main water supply point and is suitable for medium-hazard applications. It provides reliable protection against backflow caused by back-pressure and back-siphonage. Regular maintenance and testing, including backflow prevention testing, are essential to ensure optimal performance.
Double Check Valve Assembly (DCVA)
The Double Check Valve Assembly (DCVA) is a backflow prevention device that consists of two check valves separated by a tightly sealed chamber. It provides a higher level of protection against backflow, making it suitable for high-hazard applications. The DCVA is commonly used in commercial and industrial settings. Regular maintenance and testing, as required by local regulations, are necessary to ensure its effectiveness.
Reduced Pressure Zone Device (RPZD)
The Reduced Pressure Zone Device (RPZD) is the most reliable and robust backflow prevention device. It consists of two check valves and a pressure relief valve between them. The RPZD creates a zone of reduced pressure, ensuring that any backflow is contained within the device and does not contaminate the water supply. It is suitable for high-hazard applications, such as chemical plants and hospitals. Regular maintenance and backflow prevention testing, carried out by a certified professional, are vital to ensure its proper operation.
When selecting a backflow prevention device, it is important to consider the level of hazard associated with your water system. Factors such as water usage, potential contaminants, and local regulations should be taken into account.
You can read more about backflow prevention and valves on the Australian Building Codes Board
Also read more about bidets and the backflow prevention requirements.
We get often get asked to install them and home owners are surprised at what the installation requires.
How Backflow Prevention Devices Work
To effectively prevent backflow, various types of backflow prevention devices are available. Each device operates differently to ensure that the flow of water remains in the desired direction and contaminants are kept out of the water supply. Let’s explore how four common backflow prevention devices work: Atmospheric Vacuum Breaker (AVB), Pressure Vacuum Breaker (PVB), Double Check Valve Assembly (DCVA), and Reduced Pressure Zone Device (RPZD).
Atmospheric Vacuum Breaker (AVB) Operation
The Atmospheric Vacuum Breaker (AVB) is a simple and cost-effective backflow prevention device. It consists of a check valve and an air inlet valve. When the water is flowing in the correct direction, the check valve remains open, allowing the water to pass through. However, if a backflow situation occurs, the pressure differential causes the check valve to close, preventing water from flowing back into the potable water system.
Simultaneously, the air inlet valve opens, allowing air to enter the system. This introduces atmospheric pressure, breaking the vacuum and preventing the backflow of contaminated water. The AVB is commonly used for low-risk applications and is often found in residential and irrigation systems.
Pressure Vacuum Breaker (PVB) Operation
The Pressure Vacuum Breaker (PVB) is another type of backflow prevention device commonly used in residential and commercial settings. It consists of two check valves and an air inlet valve. Similar to the AVB, the PVB allows water to flow in the correct direction through the check valves.
During a backflow event, the pressure differential causes the check valves to close, blocking the reverse flow of water. At the same time, the air inlet valve opens, allowing air to enter the system and prevent the formation of a vacuum. This ensures that contaminated water cannot enter the potable water supply.
Double Check Valve Assembly (DCVA) Operation
The Double Check Valve Assembly (DCVA) is a more robust backflow prevention device commonly used in high-risk applications such as commercial and industrial settings. It consists of two independently operating check valves and test cocks for maintenance and testing purposes.
During normal water flow, the check valves remain open, allowing water to pass through. However, in the event of backflow, the pressure differential causes both check valves to close, preventing the reverse flow of water. The DCVA provides an extra layer of protection by incorporating two check valves, making it suitable for applications where a higher level of backflow prevention is required.
Reduced Pressure Zone Device (RPZD) Operation
The Reduced Pressure Zone Device (RPZD) is the most advanced type of backflow prevention device. It offers the highest level of protection and is commonly used in critical applications such as hospitals and industrial facilities. The RPZD consists of two check valves separated by a relief valve and a sensing port.
During normal water flow, the check valves remain open, allowing water to pass through. However, in the event of backflow, the pressure differential causes both check valves to close, preventing the backward flow of water. If the pressure between the check valves exceeds the set limit, the relief valve opens, discharging water through the sensing port and alleviating the excess pressure. This ensures that contaminated water cannot enter the potable water supply.
Understanding how these backflow prevention devices operate is essential for selecting the appropriate device based on the level of risk and specific application requirements.
Choosing the Right Backflow Prevention Device
When it comes to backflow prevention, selecting the appropriate backflow prevention device is crucial to ensure the safety and integrity of your water supply. There are several factors to consider when choosing the right device for your specific needs, and it is always recommended to consult with a professional plumber to determine the most suitable option.
Factors to Consider
- Type of Backflow: The type of backflow that needs to be prevented will influence the choice of backflow prevention device. Different devices are designed to handle specific types of backflow, such as backpressure or backsiphonage. Understanding the specific backflow issue you are dealing with is essential in selecting the appropriate device.
- Degree of Protection: The level of protection required is another crucial factor to consider. Some backflow prevention devices offer a higher level of protection than others. For instance, a Reduced Pressure Zone Device (RPZD) provides the highest level of protection and is typically recommended for high-risk situations. On the other hand, an Atmospheric Vacuum Breaker (AVB) may be suitable for low-risk applications.
- Local Regulations and Codes: It is important to familiarize yourself with the local regulations and codes governing backflow prevention in your area. Different regions may have specific requirements regarding the type of backflow prevention device that must be installed. Consulting with a professional plumber who is well-versed in local regulations can help ensure compliance.
- Installation and Maintenance: Consider the ease of installation and maintenance when choosing a backflow prevention device. Some devices may require more frequent testing, inspection, and maintenance than others. It is crucial to select a device that can be easily accessed and serviced to ensure its proper functioning.
Consulting with a Professional Plumber
Given the complexity and importance of backflow prevention, it is highly recommended to seek the expertise of a professional plumber. A qualified plumber can assess your specific needs, evaluate the water system, and provide recommendations tailored to your requirements. They can also guide you through the process of selecting the right backflow prevention device, ensuring that it meets all necessary standards and regulations.
By working with a professional plumber, you can have peace of mind knowing that your backflow prevention system is designed and installed correctly. They can also provide valuable insights on maintenance practices and backflow prevention testing to keep your system in optimal condition.
Remember, backflow prevention is crucial for protecting your water supply from contamination.
Maintenance and Testing
To ensure the effectiveness of your backflow prevention devices, regular maintenance and testing are essential. This helps to identify any potential issues and ensures that the devices are functioning properly. Let’s explore the importance of regular maintenance and the testing process for backflow prevention devices.
Regular Maintenance
Regular maintenance plays a crucial role in keeping your backflow prevention devices in optimal condition. Here are some key maintenance tasks to consider:
- Visual Inspection: Conduct regular visual inspections to check for any visible signs of damage, wear, or leaks. Look for cracks, corrosion, or loose fittings on the device.
- Cleaning: Keep the backflow prevention device clean and free from debris that could obstruct its operation. Remove any dirt, leaves, or other materials that may have accumulated around the device.
- Testing Ports: Ensure that the testing ports on the backflow prevention device are accessible and free from obstructions. These ports are used during testing and must be easily reachable.
- Valve Lubrication: Some backflow prevention devices have valves that may require periodic lubrication. Follow the manufacturer’s guidelines for lubricating the valves to maintain smooth operation.
- Component Replacement: If any components of the backflow prevention device are damaged or worn out, they should be promptly replaced. This includes gaskets, seals, or springs that may have deteriorated over time.
Backflow Prevention Device Testing
In addition to maintenance, regular testing it is vital to ensure their effectiveness. Testing should be performed by a certified backflow prevention tester who has the necessary knowledge and equipment. Here’s an overview of the testing process:
- Annual Testing: Backflow prevention devices should be tested at least once a year. This ensures that they are functioning properly and in compliance with local regulations. The specific testing requirements may vary depending on the type of device and local regulations.
- Testing Procedure: During testing, the backflow prevention device is subjected to simulated backflow conditions. This is done by introducing controlled pressure to the system and monitoring the device’s performance. The tester checks for any leaks, improper sealing, or pressure drops that could indicate a malfunction.
- Testing Record: After testing, a detailed report is generated, documenting the test results, any repairs or adjustments made, and the overall condition of the backflow prevention device. This record is important for record-keeping purposes and may be requested by local authorities.
Regular testing ensures that your backflow prevention devices are functioning as intended, protecting your water supply from potential contamination.
See here for more information on RPZ testing
Remember to consult with a professional plumber such as Jet Plus Plumbing to ensure proper maintenance procedures and compliance with local regulations.